Corporate
FAQ
Frequently Asked Questions
SnapQC Benchtop Vision Inspection
- The SnapQC performs all requested measurements in just 1 second.
- The measurement data can be automatically exported to your plant-wide data system, or the user may utilize the SnapQC’s built-in reports.
- Yes, the SnapQC can be utilized to measure a single item, or multiple items at once. It is the customers choice. The only difference for multiple items, is that the same average weight is assigned to all items.
- Yes, the SnapQC software can be easily configured to image the same item in a sequence of steps and all of the saved measurement data and images will be linked. An application of this feature is to measure to whole bun while viewing the crown, measure the slice of just the heel, and the bottom of the heel.
- Yes, the SnapQC can receive data from connected external devices and the user can configure the software to record grades on manual evaluations such as aroma and taste.
- Yes, contact Montrose Technologies for arrangements.
- Maintenance of the SnapQC is extremely simple. There are no moving parts, so just dust off the measurement platform from time-to-time.
There are no annual fees for SnapQC support or software updates.
Each SnapQC benchtop inspections system comes with a 2 years parts and labor warranty.
MT-Series In-line and FocalPoint Over-line Vision Inspection
- Are bottom (heel) color measurements required?
- Is individual rejection of faulty products required?
- What is the space availability?
- What is your budget?
- An overline vision system is setup to measure on an existing production conveyor. An inline vision system includes its own conveyor(s).
- An overline vision system measures size, shape, and color of products from an overhead view. An inline vision system measures these same product attributes, but is also capable of bottom (heel) color measurements.
- An overline vision system typically has no reject module but an inline vision system usually does have a reject device.
No, aside from bottom (heel) color measurements that can only be performed with an inline vision system.
An inline vision system is typically installed in one of three locations – (a) when product is partially finished, such as unglazed donuts, formed dough, and empty pizza crusts, (b) once the product is completed, after the fryer/griddle/oven/depanner, or (c) just before stacking/slicing/packaging.
Location | Benefits |
Inline Vision System Installed After Product Is Partially Finished | Remove faulty product before more ingredients are added |
Inline Vision System Installed After Product Is Completed | Quick measurement data available (do not need to wait for cooling/freezing time) that allows for equipment adjustments |
Remove faulty product before energy is spent cooling or freezing product | |
Inline Vision System Installed Just Before Packaging | Systems act like gatekeepers; able capture all faults, even those that occur during cooling/freezing (such as flipping, folding, grease spots, frozen together). |
Any location that has space.
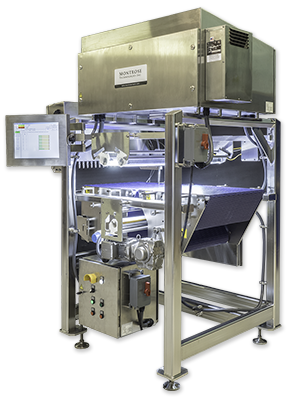